Part1. Cathode Materials for Lithium Batteries Elements
Lithium-ion batteries have become a crucial component of modern technology, powering everything from portable devices to electric vehicles. At the heart of these batteries lies the cathode, a crucial component that determines the battery’s performance, energy density, and overall efficiency. The cathode material in lithium-ion batteries plays a crucial role in electrochemical reactions that power energy storage and release. Understanding the components and compounds used in cathode materials is crucial in understanding advancements and challenges in battery technology.
One of the most commonly used cathode materials is lithium cobalt oxide (LiCoO2), which has been a staple in consumer electronics due to its high energy density and stable performance. However, the reliance on cobalt has raised concerns about cost, supply chain sustainability, and ethical mining practices. As a result, researchers have explored alternative cathode materials that reduce or eliminate cobalt while maintaining or enhancing battery performance. Among these options, lithium iron phosphate (LiFePO4) has gained prominence for its thermal stability, safety, and reduced environmental impact. Although it has a slightly lower energy density than LiCoO2, its robustness and cost-effectiveness make it a preferred choice for applications such as electric vehicles and grid storage.
Another promising cathode material is lithium nickel manganese cobalt oxide (NMC), which combines nickel, manganese, and cobalt in varying ratios to optimize energy density, power, and longevity. The versatility of NMC formulations allows manufacturers to tailor batteries for specific applications, balancing performance with cost and resource availability. Similarly, lithium nickel cobalt aluminum oxide (NCA) is another high-performance cathode material, particularly favored in the electric vehicle industry due to its high energy density and long cycle life. However, like LiCoO2, NCA relies on cobalt, which continues to drive research into cobalt-free alternatives.
In recent years, lithium-rich layered oxides and high-nickel cathodes have emerged as potential solutions to further enhance energy density and reduce costs. These materials utilize higher nickel content to increase capacity while reducing cobalt usage. However, challenges such as structural instability and thermal management must be addressed to make widespread adoption possible. Additionally, solid-state batteries, which replace liquid electrolytes with solid counterparts, are being developed to improve safety and energy density, further influencing the evolution of cathode materials.
The choice of cathode material is not solely based on performance metrics, but also on economic, environmental, and geopolitical factors. As the demand for lithium-ion batteries continues to grow, the industry must navigate the challenges of resource availability, recycling, and sustainability. Advances in cathode materials, along with advancements in manufacturing and recycling technologies, will play a crucial role in shaping the future of energy storage. By addressing these challenges, the industry can unlock the full potential of lithium-ion batteries, leading to a more sustainable and energy-efficient world.
Part2. Anode Materials Essential For Lithium Batteries
Lithium-ion batteries have become the cornerstone of modern energy storage, powering everything from portable electronics to electric vehicles. The anode is at the heart of these batteries, a crucial component that significantly impacts their performance, capacity, and longevity. The selection of anode materials is a crucial factor in optimizing lithium-ion battery technology. Graphite has become the most widely used anode material due to its stability, conductivity, and ability to efficiently intercalate lithium ions. Its layered structure enables reversible insertion and extraction of lithium ions during charge and discharge cycles, ensuring reliable performance over extended periods. Despite its widespread use, graphite is not without its limitations and researchers are continuously exploring alternative materials to overcome these challenges and enhance battery performance.
Component | Material | Advantages | Challenges | Typical Applications |
---|---|---|---|---|
Cathode | Lithium Cobalt Oxide (LiCoO₂) | High energy density, stable performance | Expensive, ethical issues with cobalt mining | Consumer electronics |
Cathode | Lithium Iron Phosphate (LiFePO₄) | Safe, thermally stable, long cycle life, environmentally friendly | Lower energy density | EVs, grid storage |
Cathode | NMC (Nickel Manganese Cobalt Oxide) | Balanced performance, tunable chemistry | Still cobalt-dependent | EVs, power tools |
Cathode | NCA (Nickel Cobalt Aluminum Oxide) | High energy density, long cycle life | Cobalt dependency, thermal management required | Premium EVs (e.g. Tesla) |
Cathode | High-Nickel & Lithium-rich Oxides | Very high capacity, reduced cobalt use | Structural instability, thermal issues | Next-gen batteries (in R&D) |
Anode | Graphite | Stable, proven, good cycle life | Limited capacity | Most lithium-ion batteries |
Anode | Silicon-based materials | Very high capacity (~10x graphite), potential for high energy batteries | Volume expansion causes mechanical stress | R&D, high-energy applications |
Anode | Lithium Metal | Highest theoretical capacity, low potential | Dendrite formation, safety risks | Solid-state battery research |
Anode | Titanium-based oxides (TiO₂, LTO) | Excellent safety, long life, fast charging | Lower capacity | EVs, grid storage, high-safety systems |
Electrolyte | LiPF₆ + Organic Carbonates (EC, DMC, EMC) | High ionic conductivity, effective SEI formation | Moisture sensitivity, flammability | Standard lithium-ion batteries |
Electrolyte | Additives (e.g., VC, flame retardants) | Improve SEI, thermal stability, and safety | Require precise formulation | All lithium-ion batteries |
Electrolyte | Solid-State Electrolytes (ceramic, polymer) | Non-flammable, enables lithium metal use, higher energy density | Interface contact, low conductivity | Next-gen batteries, in development |
One of the primary limitations of graphite is its relatively low theoretical specific capacity, which limits the amount of energy a battery can store. To overcome this, scientists have turned to silicon, a material with a significantly higher specific capacity. Silicon can store ten times more lithium ions than graphite, making it a promising candidate for next-generation anodes. However, the tendency for silicon to expand significantly during lithiation presents a significant challenge. This expansion can lead to mechanical degradation, reduced cycle life, and eventual battery failure. To address these issues, researchers are developing silicon-based composites and nanostructured designs that can adapt to volume changes while maintaining structural integrity. These advancements hold great potential for enhancing the energy density and durability of lithium-ion batteries.
Another promising anode material is lithium metal, which boasts a high theoretical specific capacity and low electrochemical potential. Lithium metal anodes have the potential to revolutionize battery technology by providing ultra-high energy densities. However, their practical use is hindered by the formation of dendrites, which grow during charging and can pierce the separator, leading to short circuits and safety hazards. To address this, scientists are exploring strategies such as solid-state electrolytes, protective coatings, and advanced separators to suppress dendrite growth and enhance the safety of lithium metal anodes. These advancements could pave the way for widespread use of lithium metal in commercial batteries.
Transition metal oxides, such as titanium dioxide (TiO₂) and lithium titanate (Li₄Ti₅O₁₂), have also gained attention as anode materials due to their excellent cycling stability and safety. These materials operate at higher voltages compared to graphite, reducing the risk of lithium plating and improving thermal stability. Although their specific capacities are lower than those of silicon or lithium metal, their robustness and long cycle life make them suitable for applications where safety and reliability are paramount, such as in electric vehicles and grid storage systems.
In conclusion, the development of advanced anode materials is crucial for pushing the boundaries of lithium-ion battery technology. While graphite remains the industry standard, materials like silicon, lithium metal, and transition metal oxides offer exciting possibilities for enhancing energy density, safety, and performance. Continuous research and innovation in this field will be crucial in meeting the growing demands for energy storage in a sustainable and efficient manner. As the search for better anode materials advances, the future of lithium-ion batteries looks brighter than ever.
Part3. Electrolyte Components Needed For Lithium Batteries
The electrolyte is a crucial component of lithium batteries, serving as the medium through which lithium ions move between the cathode and anode during charge and discharge cycles. Its composition directly affects battery performance, safety, and longevity. To fulfill its role effectively, the electrolyte must have specific properties and be composed of carefully selected materials. One of the crucial components in a lithium battery electrolyte is lithium salt, which provides the necessary source of lithium ions for ionic conductivity. Common lithium salts include lithium hexafluorophosphate (LiPF6), lithium tetrafluoroborate (LiBF4), and lithium perchlorate (LiClO4). LiPF6 is the most widely used due to its high ionic conductivity and stability within the operating voltage range of lithium-ion batteries. However, it is sensitive to moisture and can decompose at elevated temperatures, which requires careful handling and storage.
In addition to lithium salt, the electrolyte also requires a solvent to dissolve the salt and facilitate ion mobility. The solvent must have a high dielectric constant to effectively dissociate the lithium salt and have low viscosity to ensure efficient ion transport. Organic carbonates, such as ethylene carbonate (EC), dimethyl carbonate (DMC), and ethyl methyl carbonate (EMC), are commonly used as solvents in lithium battery electrolytes. These solvents are selected for their ability to form a stable solid electrolyte interphase (SEI) on the anode surface, which is crucial for preventing further electrolyte decomposition and ensuring long-term battery stability. However, the flammability of these organic solvents poses safety concerns, particularly in high-temperature or overcharging scenarios, leading to ongoing research into safer alternatives.
To enhance the performance and safety of the electrolyte, additives are often added to the formulation. These additives serve various functions, such as improving SEI formation, increasing thermal stability, and suppressing undesirable side reactions. For instance, vinylene carbonate (VC) is a widely used additive that enhances the formation of a more stable and uniform SEI layer, thereby improving cycle life and reducing capacity fade. Other additives, such as flame retardants, are added to reduce the risk of thermal runaway and enhance the overall safety of the battery. The precise selection and concentration of these additives are crucial, as they must balance performance improvements while maintaining the electrolyte’s ionic conductivity and chemical stability.
Another area of interest in electrolyte development is the use of solid-state electrolytes, which replace the liquid electrolyte with a solid material. Solid-state electrolytes have several advantages, including improved safety due to their non-flammability, higher energy density, and the potential to use lithium metal anodes. Materials such as lithium electrodes, sulfides, and polymers are being actively researched for this purpose. Nevertheless, there are still challenges in achieving high ionic conductivity and ensuring good interfacial contact between the electrolyte and electrodes.
1. What are the most common cathode materials in lithium batteries, and how do they differ?
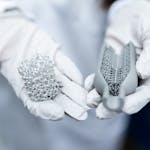
Answer: Common cathode materials include lithium cobalt oxide (LiCoO₂), lithium iron phosphate (LiFePO₄), and ternary materials (such as NMC and NCA). LiCoO₂ offers high energy density and is widely used in consumer electronics. LiFePO₄ provides excellent thermal stability and safety, making it suitable for electric vehicles and energy storage. NMC and NCA are widely used in EVs due to their high energy density, but their reliance on cobalt remains a key challenge.
2. Why is silicon considered a next-generation anode material?
Answer: Silicon has a theoretical specific capacity nearly ten times that of graphite, which can significantly boost energy density. However, it expands considerably during lithiation, which can lead to structural damage and capacity loss. To address this, researchers are developing silicon-based composites and nanostructured designs that can better accommodate volume changes and improve cycle life.
3. What are the main components of lithium battery electrolytes and their roles?
Answer: Solid-state batteries use solid electrolytes, offering higher safety (non-flammable), greater energy density, and the potential to use lithium metal anodes. However, they face challenges such as low ionic conductivity and poor interfacial contact between the solid electrolyte and electrodes, which require further advancements in materials and interface engineering.
4. What are the advantages of solid-state batteries, and what challenges do they face?
Answer: Solid-state batteries use solid electrolytes, offering higher safety (non-flammable), greater energy density, and the potential to use lithium metal anodes. However, they face challenges such as low ionic conductivity and poor interfacial contact between the solid electrolyte and electrodes, which require further advancements in materials and interface engineering.
5. Why is reducing or replacing cobalt in cathode materials important?
Answer: Cobalt is expensive, has limited availability, and is primarily sourced from regions with supply chain risks and ethical mining concerns. Therefore, the industry is shifting toward low-cobalt or cobalt-free materials, such as high-nickel NMC and cobalt-free LiFePO₄, to reduce costs, improve sustainability, and ensure more stable production capacity.