Polymer electrolytes are mainly divided into Solid Polymer Electrolytes (SPEs), Gel Polymer Electrolytes (GPEs), and porous SPEs. Next, this article will further investigate the specific polymer materials and lithium salts used in these different types of electrolytes, as well as their advantages and disadvantages in terms of ionic conductivity, mechanical strength, thermal stability, and safety.
1. Definition and Core Characteristics of Lithium-Ion Polymer Batteries
Lithium-Ion Polymer Batteries, as the name implies, have “polymer” at their core. The biggest difference from the liquid lithium-ion batteries we commonly see lies in the fact that their electrolyte is no longer a free-flowing liquid but is based on solid or gel-like polymer materials. This change in form directly brings significant advantages to polymer lithium batteries in terms of safety and design flexibility.
1.1 Innovation in Electrolyte Morphology
Traditional liquid lithium batteries are filled with flammable liquid electrolytes. Once the battery experiences abnormal conditions such as a short circuit or overcharge, it can trigger violent chemical reactions, leading to combustion or even explosion. Polymer lithium batteries, on the other hand, fundamentally reduce this risk by using solid or gel-like polymer electrolytes.
Specifically, polymer electrolytes are mainly divided into the following types:
Solid Polymer Electrolytes (SPE): This type of electrolyte is composed entirely of polymer materials and does not contain any liquid components. Its advantage is extremely high safety, but its ionic conductivity is relatively low, especially at room temperature, which to some extent limits its application in high C-rate charge and discharge scenarios. Early polymer lithium batteries mostly used SPEs, but with technological advancements, pure solid-state polymer batteries are no longer common in consumer electronics and are more often used in specialized fields with extremely high safety requirements.
Gel Polymer Electrolytes (GPE): To balance safety and ionic conductivity, engineers developed Gel Polymer Electrolytes. This type of electrolyte involves injecting a small amount of liquid electrolyte into a polymer framework to form a gel network. This maintains a high ionic conductivity while significantly reducing the amount of liquid electrolyte, thereby improving safety. The vast majority of polymer lithium batteries on the market today use GPEs.
Semi-Polymer Batteries: This type of battery does not entirely use a polymer electrolyte but instead coats a layer of polymer material (such as PVDF polyvinylidene fluoride) on the traditional separator. This coating can enhance the mechanical strength of the separator and its adhesion to the electrodes, helping to inhibit internal short circuits and thus improve safety.
All-Polymer Batteries: This type of battery, based on semi-polymer batteries, further mixes the electrode materials with polymer binders to form a more compact structure. This design can reduce the use of liquid electrolytes and improve the overall stability of the battery.
From DataPower‘s 16 years of generation and manufacturing experience, GPEs are currently the mainstream choice for polymer lithium batteries, striking a good balance between safety, energy density, and cost. Pure solid-state polymer batteries, although extremely safe, still face some technical challenges in industrialization and large-scale application, such as how to further improve their ionic conductivity at room temperature.
1.2 Unique Structural Design: Pouch Cell
Another significant feature of the structural design of polymer lithium batteries is the use of an aluminum-plastic composite film as the outer casing, which we commonly call a “pouch cell.” This pouch material usually consists of a multi-layer structure, such as PP (polypropylene), Al (aluminum), nylon, etc., with each layer having its specific function: the PP layer mainly acts as a heat seal to ensure the battery’s hermeticity; the aluminum layer is a barrier layer that can effectively prevent moisture and air from entering the battery, protecting the cell materials; the nylon layer provides a certain degree of mechanical strength.
Compared to the metal casings used in traditional liquid lithium batteries, pouch cells have the following distinct advantages:
Lightweight and Thin: The pouch material itself is lighter than metal, and it does not require the extra strength redundancy of metal casings, so it can be made thinner and lighter. This is crucial for portable electronic devices that strive for lightweight and thin designs. I once participated in the battery design of an ultra-thin mobile phone, and the thickness requirement for the battery was very strict. Ultimately, we chose a polymer pouch cell to achieve this.
Flexibility: Pouch materials have a certain degree of flexibility, which can adapt to the needs of devices with special shapes, such as wearable devices and flexible displays. This provides designers with greater imagination to create various irregularly shaped electronic products.
Enhanced Safety: When an internal abnormality causes gas generation, a pouch cell will bulge and deform instead of easily exploding like a metal casing. This “gassing” characteristic can effectively release internal pressure and reduce safety risks. Of course, this does not mean that polymer batteries are absolutely safe, but under the same conditions, their safety is indeed higher than that of liquid batteries.
Customizable Shape: The manufacturing process of pouch cells is relatively flexible and can be customized into various shapes, such as trapezoidal or ultra-thin card shapes, according to different device requirements. This provides convenience for some special application scenarios.
Of course, pouch cells are not perfect. Their mechanical strength is relatively weaker than that of metal casings, making them susceptible to puncture by sharp objects. Therefore, when using devices powered by polymer batteries, we need to be careful to avoid squeezing or puncturing the battery.
1.3 Performance Advantages: Energy Density, Cycle Life, and Self-Discharge
Polymer lithium batteries also exhibit unique advantages in terms of performance:
Comparison Dimension | Lithium-Ion Polymer Battery | Liquid Lithium-Ion Battery | ||
---|---|---|---|---|
Electrolyte | Solid/gel polymer electrolyte, some contain a small amount of liquid components | Liquid electrolyte (flammable) | ||
Safety | Not prone to explosion, often manifests as bulging when faulty | Relatively poor safety, may explode in extreme cases | ||
Shape and Thickness | Ultra-thin (<1mm), customizable to any shape | Generally thicker, fixed shape | ||
Weight and Capacity | 10%-15% higher capacity and 20%-40% lighter in the same volume | Capacity and weight are limited by the metal casing | ||
Voltage and Combination | Single cell can achieve higher voltage (multi-layer structure) | Multiple cells need to be connected in series to achieve high voltage | ||
Cost | Higher manufacturing cost (complex technology) | Lower cost, mature technology | ||
Application Fields | Portable devices, high safety requirement applications, special-shaped devices, flexible electronics, etc. | Mid-to-low-end consumer electronics, electric vehicles, energy storage systems, etc. |
Higher Energy Density: Due to the use of lighter and thinner pouch structures and the ability to optimize electrolyte and electrode materials to increase energy density, polymer lithium batteries can typically achieve 10%-30% higher energy density than traditional liquid batteries in the same volume or weight. This means that with the same device size, longer battery life can be achieved. This is very important for portable devices such as mobile phones and laptops.
Lighter Weight: Without the heavy metal casing, the weight of polymer lithium batteries is usually 20%-40% lighter than that of liquid batteries. This is a huge advantage for weight-sensitive applications such as drones and wearable devices.
Longer Cycle Life: Polymer lithium batteries can usually achieve more than 500 charge-discharge cycles under normal usage conditions. Some high-end polymer batteries can even reach more than 1000 cycles. Moreover, polymer batteries have a low self-discharge rate, and even if they are not used for a long time, they will not lose too much power. In addition, polymer lithium batteries usually have no memory effect and can be charged at any time without needing to be fully discharged first.
Of course, these performance indicators will also be affected by various factors such as the specific design, manufacturing process, and usage conditions of the battery. However, overall, polymer lithium batteries have certain advantages in terms of energy density, weight, and cycle life.
2. Subsequent research directions for lithium-ion polymers should focus on the following aspects:
Key Steps in Manufacturing Processes
To help you have a clearer understanding of the manufacturing process of lithium-ion polymer batteries, key steps include mixing electrode materials, coating and drying, calendering, slitting and stacking or winding, lamination, electrolyte injection, sealing and packaging, formation, and testing. The manufacturing process for pouch cells is similar but differs in cell assembly and packaging. Vacuum baking is crucial for controlling moisture. Electrode preparation involves mixing active materials, conductive agents, and binders into a slurry, which is then coated onto current collectors. Solvent-free manufacturing methods are also being explored to reduce costs and environmental impact. Polymer batteries typically have gel electrolytes injected, and pouch cell assembly often uses electrode sheet and separator lamination technology. The main differences from liquid batteries lie in the use of solid or gel polymer electrolytes and flexible packaging.
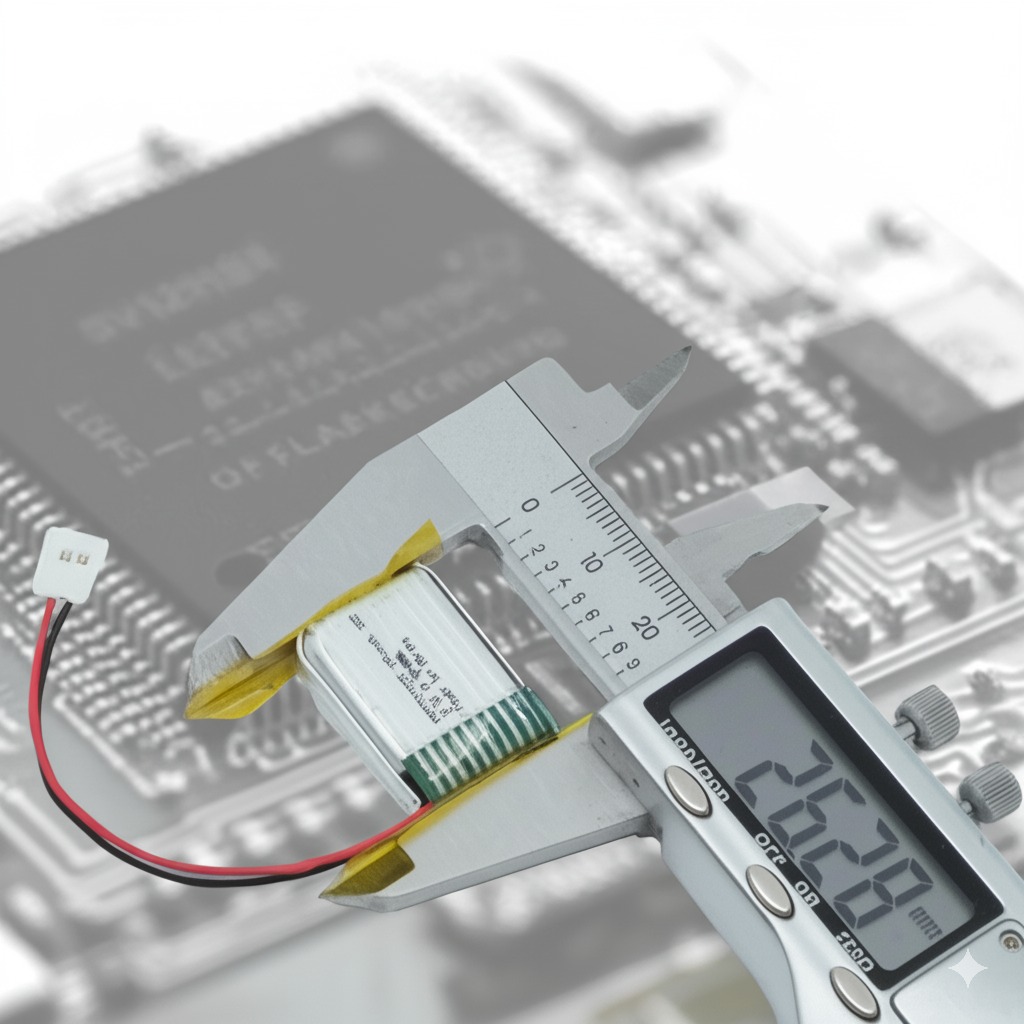
Wide Range of Applications
lithium-ion Polymer batteries, due to their lightweight and high energy density characteristics, are widely used in portable devices such as smartphones, laptops, tablets, and wearable devices. In the medical field, they power portable monitors, implantable devices, and diagnostic tools, benefiting from their compact size, high energy density, and long cycle life. Drones also rely on the high energy density and lightweight nature of polymer batteries for longer flight times and higher payloads. Flexible electronics, such as wearable sensors and flexible displays, utilize the flexibility and ultra-thin profile of polymer batteries. These applications all benefit from the flexibility, light weight, high energy density, and higher safety compared to traditional liquid batteries.
Important Safety Standards
Regarding safety standards and regulations, IEC 62133 and UL standards (such as UL 1642, UL 2054, UL 2580) are key references. These standards cover multiple safety aspects such as overcharge, over-discharge, short circuit, thermal runaway, and mechanical integrity. UN 38.3 is crucial for safety testing during the transportation of lithium batteries. Taking appropriate safety measures during handling, charging, storage, and disposal, such as using appropriate chargers, avoiding extreme temperatures, preventing short circuits, and properly disposing of them as hazardous waste, is essential to prevent fires or explosions. Overcharge, over-discharge, short circuit, and puncture tests are standard safety assessment items for lithium-ion polymer batteries.
Key Performance Parameters
The energy density of lithium-ion polymer batteries typically ranges from 100-265 Wh/kg and 250-670 Wh/L, generally higher than traditional lithium-ion batteries. The cycle life is typically between 800-2000 cycles, often longer than standard lithium-ion batteries. The charge-discharge rate can be high, with some polymer batteries supporting fast charging (2-3C). The operating temperature range is usually between -20°C and 70°C, with some high-temperature models capable of withstanding even higher temperatures. Extreme temperatures can affect battery performance and lifespan. The latest research mainly focuses on improving energy density, cycle life, and safety by improving materials (electrolytes, electrodes), battery design, and manufacturing processes.