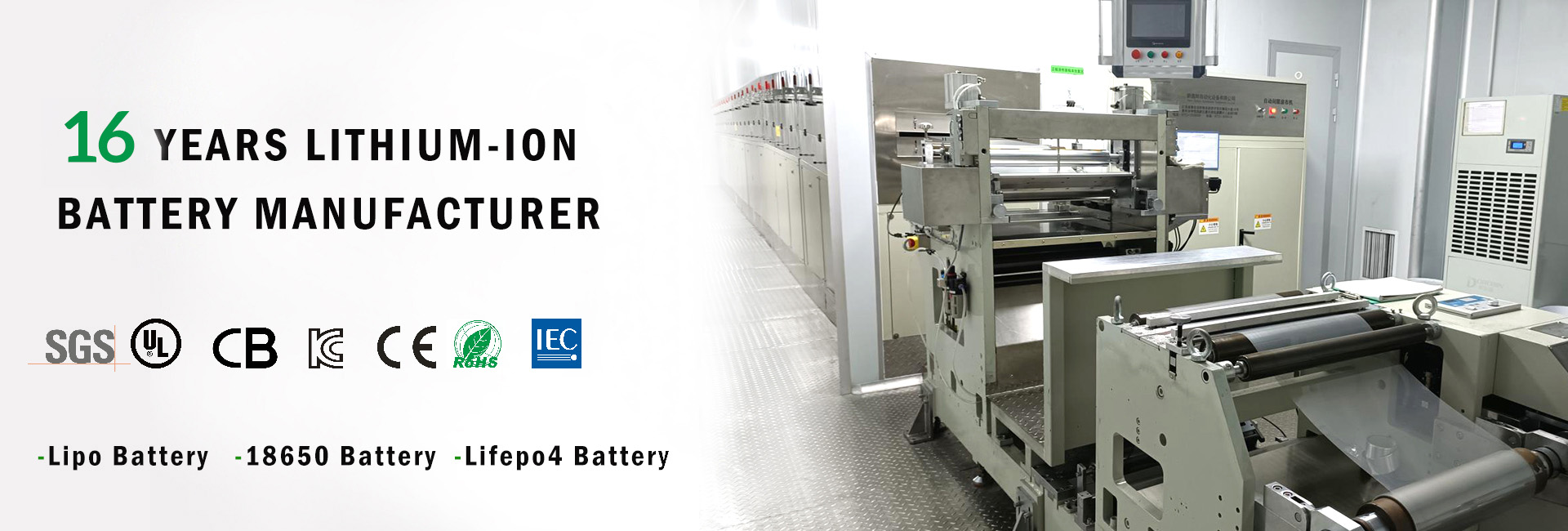
Lithium-polymer (LiPo) batteries are the lifeblood of modern electronics, powering everything from smartphones and drones to electric vehicles and renewable energy storage systems. But with global demand surging (projected to grow at a CAGR of 15.4% through 2030), selecting the right manufacturer has never been more critical—or more complex. The stakes are high: a subpar battery can derail product performance, safety, and your brand’s reputation.
This guide cuts through the noise, equipping you with actionable insights to evaluate manufacturers, avoid common pitfalls, and build partnerships that fuel innovation.
Why Your Choice of Manufacturer Matters
Lithium-polymer batteries aren’t commodities. Their performance hinges on chemistry nuances, manufacturing precision, and rigorous safety protocols. Consider this:
- A 1% defect rate in battery cells can lead to recalls costing millions.
- Energy density (the amount of power stored per unit volume) varies by up to 20% across manufacturers, directly impacting product design.
- Supply chain delays or quality inconsistencies can stall production lines, costing companies $1M per day in lost revenue.
The right manufacturer isn’t just a supplier—it’s a strategic partner in your product’s success.
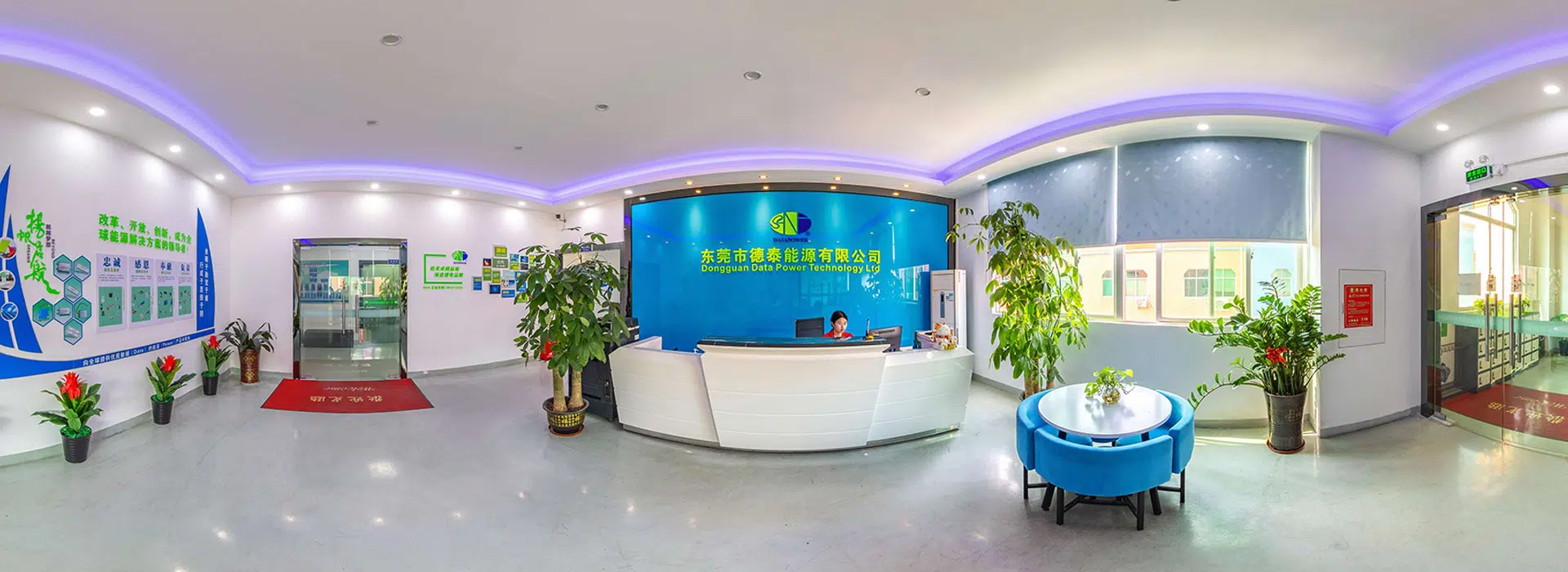
Key Factors to Compare Manufacturers
1. Technical Expertise & Innovation
Look for manufacturers invested in R&D. For example, Samsung SDI and LG Chem allocate over 5% of annual revenue to battery research, driving breakthroughs like silicon-anode technology for higher energy density. Ask:
- Do they publish whitepapers or hold patents in LiPo innovation?
- Can they customize electrolytes or cell architectures for your needs?
2. Certifications & Compliance
Certifications are non-negotiable. Prioritize manufacturers compliant with:
- UL 1642 (safety standard for lithium batteries)
- IEC 62133 (international safety requirements)
- REACH/RoHS (EU environmental regulations)
A manufacturer lacking these may expose you to legal risks or market-entry barriers.
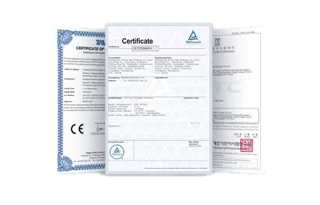
3. Scalability & Supply Chain Resilience
In the wake of pandemic-driven shortages, 52% of electronics firms now prioritize suppliers with diversified raw material sourcing. Evaluate:
- Production capacity: Can they scale from prototypes to mass production?
- Location: Proximity to your market reduces logistics costs (e.g., CATL dominates Asia, while Tesla’s Gigafactories focus on regional supply).
4. Transparency & Testing Protocols
Reputable manufacturers provide cycle life data, thermal abuse test results, and batch traceability. For instance, Panasonic shares detailed discharge curves and aging profiles for its EV batteries. Avoid vendors who withhold technical documentation.
The Manufacturer Comparison Table
Use this table to shortlist candidates:
Criteria | Low-Tier Manufacturer | Mid-Tier Manufacturer | Top-Tier Manufacturer |
R&D Investment | <1% of revenue | 2-3% of revenue | 5%+ of revenue |
인증 | Basic (CE, FCC) | UL, IEC | UL+IEC+UN38.3+AEC-Q200 (auto) |
Cycle Life (Guaranteed) | 300–500 cycles | 500–800 cycles | 1,000+ cycles |
Lead Time | 8–12 weeks | 6–8 weeks | 4–6 weeks (with buffer stocks) |
Customization | Limited (standard sizes) | Moderate (electrolyte tweaks) | Full (cell shape, chemistry) |
Sources: Industry benchmarks from Intertek and Battery Power Online.
The Hidden Risks of Cost-Driven Decisions
While budget constraints are real, opting for the cheapest bidder often backfires:
- Cycle life vs. cost: A $0.50/Wh battery with 500 cycles equals $0.001/cycle. A $0.70/Wh battery with 1,200 cycles costs $0.00058/cycle—42% cheaper long-term.
- Safety incidents: Between 2016–2021, faulty batteries caused 23% of consumer electronics recalls.
Case in Point: A drone startup chose a low-cost manufacturer to save $3/unit. Post-launch, 15% of batteries swelled due to poor electrolyte formulation, costing $2M in replacements and reputational damage.
Future-Proofing Your Partnership
The LiPo industry is evolving rapidly. Manufacturers leading in these areas will future-proof your supply chain:
Solid-State Batteries
Firms like QuantumScape are pioneering solid-state LiPo batteries with 2x energy density and reduced flammability. Partnering with innovators ensures access to next-gen tech.
Sustainability Practices
With the EU’s Battery Regulation 2023 mandating recycling efficiency and carbon footprint disclosures, align with manufacturers using recycled materials (e.g., Redwood Materials partners with Panasonic to recover lithium and cobalt).
AI-Driven Quality Control
Leading factories now use AI to inspect electrode coatings and detect microscopic defects, reducing failure rates by 30%. Ask if your supplier employs machine learning in production.