As the electric device industry matures, reducing costs and optimizing high-volume production have become top priorities for
both device manufacturers and battery makers. Currently, batteries remain the most expensive component in most devices, presenting a significant business opportunity.
Part 1: Optimize the assembly
This paper focuses on how to optimize the assembly and lamination processes of electric device battery cell tabs to increase
production efficiency, thereby increasing battery production and reducing battery costs.
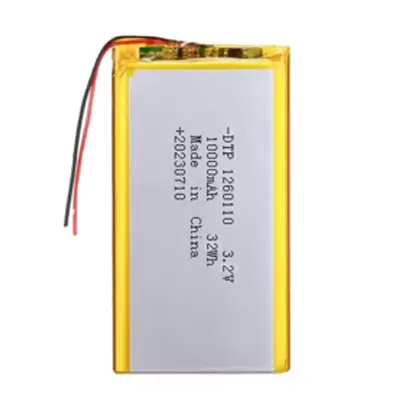
Part 2 : cell connection system (CCS) Assembly methods
As the name implies, a cell connection system (CCS) is a critical component that collects the output power of individual battery
cells and converges the current for transmission to the powertrain of an electric device.
A CCS typically consists of a set of conductive plates or foils (usually made of copper or aluminum). These conductive plates or foils are bonded to individual battery cells, forming a low-resistance path for energy transfer to the external battery circuit.
As shown in Figure 1, there are typically three assembly methods for CCS design.
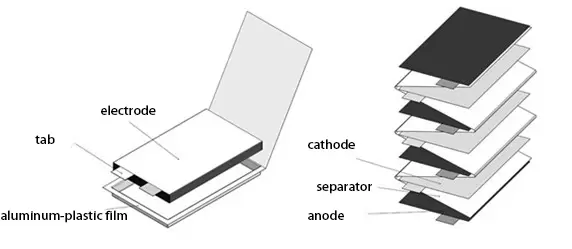
In the past, the advantage of the plastic tray method was that it could help to accurately position the cells, keep the cells
aligned with the welding points, and provide continuous positional stability.
However, most modern electric device battery designs and cell-to-pack applications currently achieve cell positioning using foam, adhesives, or other methods, making the plastic tray method less important for cell positioning.
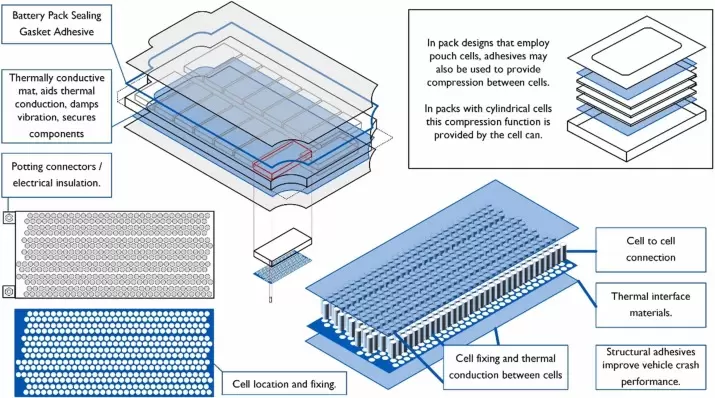
The evolution of CCS assembly methods
has provided more options for electric device and battery manufacturers in battery component design and manufacturing. However, more choices can sometimes lead to delays in front-end work if the pros and cons are not clearly weighed.